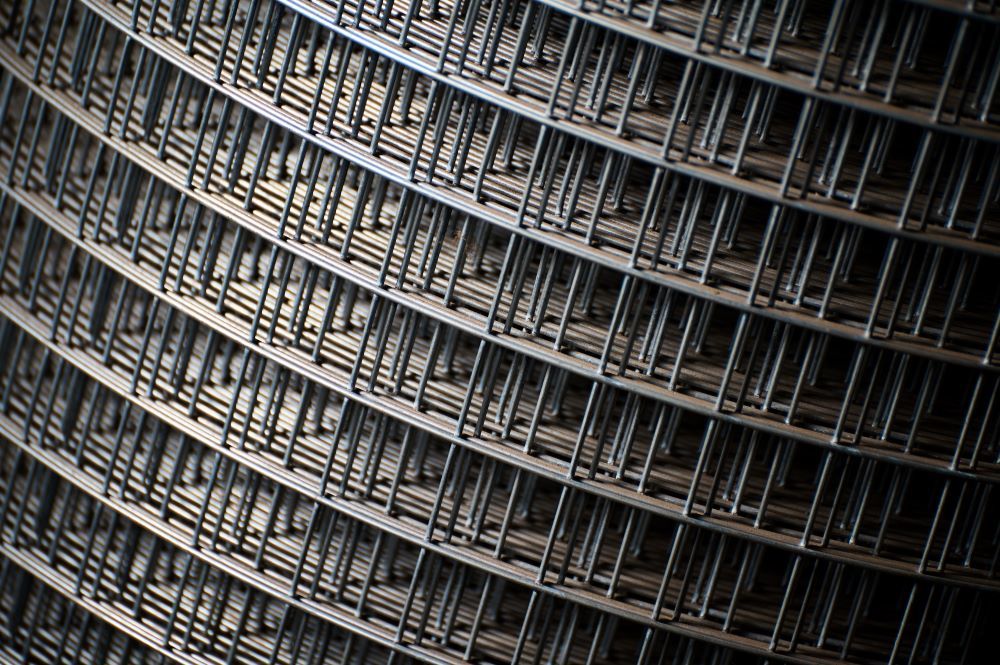
The process of manufacturing weldmesh: A behind the scenes look
Manufacturing weldmesh involves several intricate steps to create a durable and versatile product used in various industries like construction, agriculture, fencing, and more. Here's a behind-the-scenes look at the process:
- Raw Material Selection: The process begins with the selection of raw materials. Typically, weldmesh is made from high-quality steel wire. The wire may vary in diameter depending on the intended use and specifications of the final product.
- Wire Drawing: The selected steel wire undergoes a wire drawing process where it's pulled through a series of progressively smaller dies to reduce its diameter and improve its tensile strength. This step ensures uniformity and consistency in the wire's thickness.
- Mesh Formation: The drawn wire is then fed into a mesh welding machine. This machine consists of multiple longitudinal wires (called line wires) and cross wires. The wires intersect at right angles and are welded together using electric resistance welding. The machine is programmed to create the desired mesh pattern and dimensions.
- Welding Process: Electric resistance welding is commonly used in weldmesh manufacturing. In this process, an electric current passes through the intersecting wires, generating heat that melts the wire surfaces. Pressure is applied to forge the wires together, forming strong and durable weld joints.
- Trimming and Straightening: Once the mesh is welded, it undergoes trimming to remove excess material and achieve uniform edges. The mesh is then passed through straightening rollers to ensure it lies flat and maintains its shape.
- Surface Treatment: Depending on the intended application, the weldmesh may undergo surface treatments such as galvanization or powder coating to enhance its corrosion resistance and durability. Galvanization involves coating the mesh with a layer of zinc to protect it from rust and corrosion.
- Quality Control: Throughout the manufacturing process, quality control measures are implemented to ensure the weldmesh meets the required standards. This may involve visual inspections, dimensional checks, and mechanical testing to verify strength and integrity.
- Packaging and Distribution: Once the weldmesh passes quality control checks, it is packaged according to customer specifications and prepared for distribution. This may involve rolling the mesh onto spools, cutting it into panels, or bundling it into coils for easy transportation and handling.
Overall, the manufacturing process of weldmesh requires precision machinery, skilled labor, and stringent quality control to produce a reliable and high-quality product suitable for a wide range of applications.